Types of Roof Coatings
Roof Coatings are a cost-effective solution for commercial property owners that want to save on labor costs and improve the aesthetic of their roof. They are also sustainable, allowing you to re-coat your roof every 10+ years, lengthening the life of your roof and preventing costly repairs.
Acrylic coatings are typically solvent-based and come in two main types, aromatic (less UV stable) and aliphatic (very UV stable). They have good mechanical properties and high abrasion resistance.
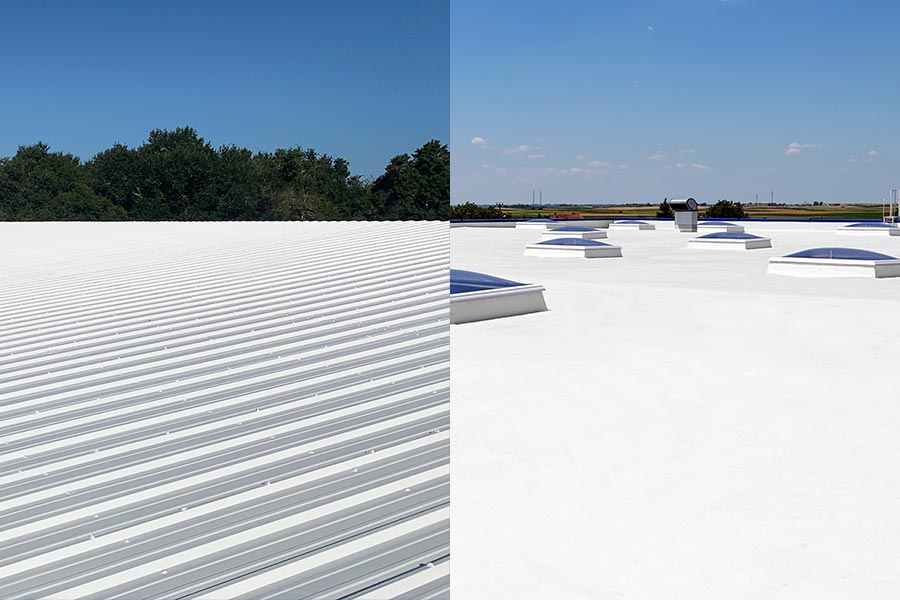
Acrylic
Acrylic roof coatings are a popular choice for commercial flat roofs. They are compatible with a wide range of substrates including modified bitumen, metal, single-ply, built-up, and spray polyurethane foam.
They are cost-effective, easy to work with, and can last for 20 years or more. They are a great option for any building owner or contractor who wants to extend the life of a roof. They can be used on new construction or re-roofing jobs.
These roof coatings are also highly reflective, which means they reflect UV light and can prevent premature degradation of roofing materials. This helps save building owners money on energy costs and can help protect the environment as well.
In addition to providing UV protection, acrylic roof coatings are very durable and extend the life of existing roofs. They are designed to withstand heavy weights, inclement weather, and other factors that can damage your roof.
They also are very dirt resistant and maintain their appearance over time, preventing a dull looking surface. This can make your roof stand out more on the exterior, increasing the value of the building and boosting curb appeal.
Another benefit of these roofing coatings is their ability to keep water out of your roof. Leaks can cause mold growth, deterioration of insulation and other structural issues.
Additionally, ponding water can have a huge impact on the integrity of your roofing material. If water begins to pool, it can cause your roof to crack and deteriorate quickly.
When choosing a coating, it’s important to know how well the product will perform in a ponding-water scenario. It’s imperative to speak with a specialist before purchasing the product, and determine which one will best stand up to these conditions.
A common question among commercial roofers is which roofing coatings are better for ponding water. While both silicone and acrylic have similar performance in this situation, they do have different weaknesses.
If your commercial building has a lot of ponding water, it may be worth considering silicone coatings. These products are specially designed to withstand the amount of ponding water that your roof experiences.
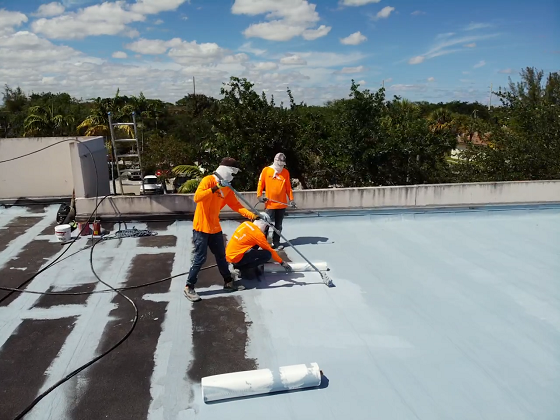
Silicone
Silicone coatings are a type of roof coating that can be applied over many different types of roofing materials. They are a great option for those looking to protect their commercial buildings from the elements, and they are also cost effective when compared with other options.
One of the major benefits of using silicone for your roof is that it will help prevent water from getting into your building. This will reduce the risk of mold and mildew in your facility. In addition, it will keep the temperature inside your building at a more comfortable level.
Another reason to consider using a silicone roof coating is that it will help to extend the life of your roof. This can help you save money on repairs down the road, as well as on your energy bills.
It can also prevent hail from damaging your roof, which can be a huge pain to deal with. In addition, it can protect your building from ice dams, and it can help to prevent rainwater from seeping into your structure.
You should not use this roof coating if you have any areas where there is heavy foot traffic or abrasion on your roof. In these situations, you will need to look at other options for your roof coating.
The downside to using silicone for your roof is that it will attract dirt and other airborne particles from the air. Over time, this will cause the silicone to lose its reflective properties and become more susceptible to heat from the sun.
In these cases, it is recommended to power wash the area regularly. This will remove the dust from the area and help to improve the performance of the silicone roof coating.
A high-solids 100 percent silicone roof coating can be used on a wide variety of substrates, including asphalt, polymer-modified bitumen, metal, concrete, TPO, PVC and EPDM. In addition, it is solvent-free and meets all VOC-related regulations. Ultimately, this makes it an excellent choice for hospitals, schools and other buildings where employees may be highly sensitive to fumes.
Polyurethane
Urethane coatings are among the strongest and most durable elastomeric roof coatings available. They are most commonly used to coat sprayed-in-place polyurethane foam insulation as well as commercial roofing substrates including modified bitumen, single-ply, EPDM, smooth/gravel BUR, and concrete roof decks.
These durable, flexible monolithic membrane layers can effectively withstand the daily expansion and contraction (thermal movement) of roof structures as well as the damaging effects of ponding water. They also have excellent impact-resistant properties, making them ideal for use on commercial roofs with heavy pedestrian traffic.
They are incredibly versatile and come in a variety of finishes for both commercial-architectural and residential applications. They can be applied by brush, roller or spray. They are available in metallic, pearl and solid color finishes across the full spectrum of sheens from gloss to matte/flat.
Polyurethane roof coatings are extremely durable and are highly resistant to the corrosive effect of UV radiation. They can help prevent the deterioration of the membrane beneath them and may even extend the life of your roof.
Their reflective properties also help keep the building cool. However, they attract dirt and tend to lose their reflectivity over time when not cleaned regularly.
In addition, they can be very slippery when moisture is present. This is why we often recommend the use of mineral granules to be added to these coatings to reduce friction between the membrane and the surrounding surface.
Using a polyurethane coating to protect your roof is a great way to ensure that it stays protected and will save you money in the long run by preventing costly repairs or replacements. In fact, it can even extend the life of your roof by avoiding ponding water and preventing leaks.
If you’re ready to see how your roof could benefit from a new coating, get in touch with a qualified contractor who can assess the condition of your existing roof and help you choose the right product for the job. They will be able to advise you on the best type of polyurethane for your needs and give you more information about the installation process.
Fluid-Applied Asphaltic Rubber Membrane System
The Fluid-Applied Asphaltic Rubber Membrane System is a cold process liquid applied membrane that combines the elastic properties of rubber with the waterproofing/weatherproof characteristics of an emulsified asphalt. It forms a properly adhered monolithic, seamless membrane that provides instant waterproofing/weatherproofing capabilities.
It can be applied vertically up to 200 mils thick in one application, and it can be re-applied as needed. The membrane can be applied over concrete, steel or masonry surfaces and will resist corrosion due to its natural UV-resistant properties. It is compatible with all types of coatings and can be used for all surfacing requirements including pavers, living plants, green assemblies, poured concrete and more.
Unlike coatings that only provide a film surface or adhesives that require reinforcements for waterproofing capacity, the liquid rubber forms an instant, seamless membrane that is fully adhered and cured in seconds to 80 percent of its full strength. This unique feature enables a continuous system application without the need for separate components that may break down over time, as happens with multi-component systems.
This unique material is a two-part formulation that is spray mixed at the time of application by a specially designed spray rig and a catalyst. When the liquid rubber and the catalyst come into contact, it reacts to form an elastomeric, seamless membrane that is fully adhered and instantly cured to 80 percent of its strength.
It is a low-cost, fast-setting membrane that can be used as a direct replacement for hot-applied built-up roof systems. The material is available in either an asphalt-based or coal-tar-based composition, and it can be used on all types of roofing substrates including pre-existing BUR, a variety of decking materials, concrete slabs, wood and metal joists and more.
Another key feature of the liquid rubber membrane is its superior elongation and recovery. It has an elongation and flexibility that exceeds industry standards, and it recovers to 90 percent of its original shape after elongation. It also performs in extreme cold/heat conditions that would damage other adhesives and coatings.
This is the perfect solution for all commercial waterproofing applications. It is cost-effective, durable and has long-term warranties. It is easy to install and offers many benefits over other membranes, such as elongation and flexibility, high adhesion rates and low water absorption rate. It is a great alternative to sheet membranes and can save up to 60% in labor costs.